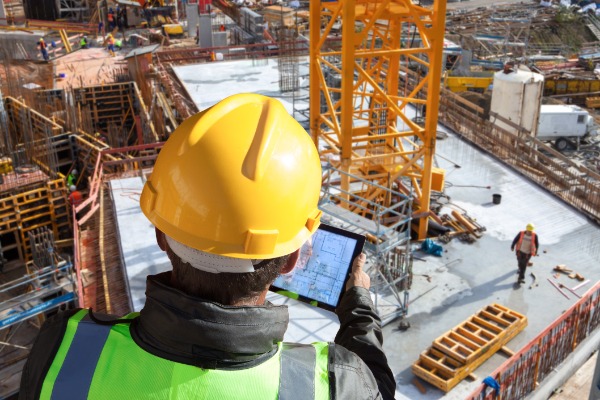
This blog was published in conjunction with RICS World Built Environment Forum.
A lack of data management and sharing can result in significant additions to the total cost of construction projects. How does the management and sharing of data on some construction projects fall short?
Construction projects consume vast amounts of data, down to the quantities of nuts and bolts on a drawing or engineer's plan.
From foundation to roof, the build processes and procedures are fairly standard across most organizations. Yet the management and sharing of data among the multiple stakeholders, supply chains and delivery teams working on a project frequently fall short. Without some form of process or standard, data and information on construction projects can often become unstructured and difficult to search and share.
This lack of efficiency could add 20-25% to the cost of a project, according to figures cited by Asite’s Uncovering the ROI in a Common Data Environment.
The Key to Adoption
For systems to be successful, they must be user-friendly and possess a degree of rigidity. This is to ensure data is entered in a consistent way, while also allowing the flexibility that changing requirements demand.
Many of the problems with the widespread adoption of an IT system stem from an initial perception that the system is “too hard to learn” or “not intuitive”. People revert to sharing data through other means, such as email or on-site printed drawings. To engage with the supply chain effectively, construction projects must adopt a robust but easy-to-use protocol.
The Best of Both Worlds
Some of the most successful projects are those where subcontractors are contractually obliged to use a specific system.
Until there is a common data standard that everybody uses, setting up a parallel system provides a halfway house to achieving adoption and integration. Data is entered on the system in adherence to the client’s protocols and standards.
Third parties can also store data alongside those files, for example, using their own naming conventions. This effectively offers the best of both worlds – giving the capability to search through the originator’s information and/or across system-wide information stored as well.
Getting Off to the Right Start
When implementing a new system, a common mistake is procuring the system too late in the project lifecycle, creating undue pressure and increasing the risk of mistakes occurring. IT teams also need to be involved in the process.
Often systems are controlled and owned by a project or a design management team. While this is not wrong in principle - as the system is a design and project management tool - being part of the business’ systems architecture will generate a better return on investment.
"Digitalisation can go a long way to improving productivity and efficiency in construction, increasing the likelihood of getting it right first time, and reducing the chance of project errors and delays."
Data and Red Flags
According to solutions provider Emerson, up to 30% of initial data created during the design and construction phases is lost by the time of project closeout. If a company can interrogate data from completed projects, including budgets, costs, overruns and changes, there is the potential to generate powerful insight into how the business is operating and what can be expected moving forward based on predictive analytics.
Furthermore, ensuring consistent data is going into a project can provide key insights into how the project is progressing. If a company knows the size, cost and duration of a project and the quantity of data it usually expects to receive, changes in normal patterns can raise red flags. For example, if there are more revisions than expected, the customer may be making too many alterations, affecting the cost of the project. Conversely, if not enough data is being received, this could indicate an issue with the design team or an indecisive customer, again increasing cost and leading to delays.
Construction’s Unique Challenges
The construction industry has been labeled unproductive compared to other sectors, and lack of digitalization and standardization are among the main reasons.
Construction projects can often adopt technology in a somewhat chaotic fashion, due to the speed of change and the necessity to get projects built as quickly as possible. For the customer and contractor, this lessens the ability to embed technology properly. In an industry working to tight margins and deadlines, any issues must be addressed on site. In comparison, the aerospace and automotive industries spend years developing a product, getting everything right upfront. They are also better financed in respect of research and development and in providing the right machines and tools for production.
The pandemic may have led to a slower pace in the construction industry, allowing companies more time to prepare and incorporate technology. The industry phase some years ago of ‘just-in-time design’, for example, worked well when projects went to plan but didn’t provide the latitude to resolve errors in the most satisfactory manner.
Talking to Each Other
Digitalization can go a long way to improving productivity and efficiency in construction, increasing the likelihood of getting it right the first time, and reducing the chance of project errors and delays. But without standards, it is difficult to integrate and share data. And in today’s electronic world, for systems to talk to each other, we need standards.
Want to learn more about how data management can improve your construction projects? Discover more here.
Richard Harrison
Director of Customer Success at Asite
Asite Insights in your inbox.
Sign up for product news and our latest insights published monthly. It's a newsletter so hot, even global warming can't keep up.