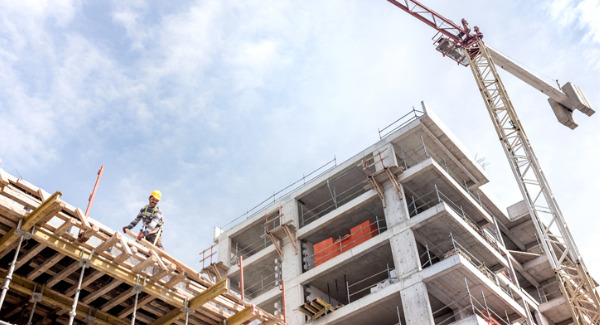
Whether you blame it on the shipping container shortage or bored homeowners leaning into their DIY projects, the construction industry has likely not seen the last of rising material prices.
With material costs at all-time highs, three major factors are driving up prices and causing chaos on today’s construction sites.
For starters, strong demand and supply chain issues combined with limited distribution are driving inflationary pressure. Strong demand is largely due to countries around the globe investing in infrastructure construction as a strategy to revitalize their economy. As countries “build back better” in response to the pandemic, the demand for construction materials increases.
Secondly, producers of these building products have experienced and continue to experience work stoppages or decreased productivity due to health protocols or government restrictions.
Lastly, there is a shipping container shortage. Even if building materials are produced in a timely manner, they may not get loaded onto a boat for weeks. One port in China—the third busiest in the world—had been shut down for weeks due to Covid. Ports in California—which are responsible for one-third of all U.S. imports—are seeing record numbers of ships waiting to dock. The reason? The ports don’t have the capacity to process the cargo at the speed it’s arriving.
Stockpiling of cargo containers combined with overall global demand has increased cargo prices exponentially, especially between Asia and North America.
Material Shortages Make Bidding Tough
How bad is it for contractors? The cost of building materials is rising and fluctuating to a degree where contractors can no longer accurately quote projects they are trying to bid and win. This is because the price of the building materials at the time it is purchased will be higher than when the project was at the bidding stage.
For example, if a contractor uses the current prices for their bid, they may set themselves up to lose significant revenue when they purchase the materials six months from now. Meanwhile, they will likely lose contracts when bidding on new jobs if they use the cost they expect the materials to be in six months.
Furthermore, shortages are complicating construction schedules. For example, materials such as windows, insulation, air conditioners, and other items are on back-order or have become unavailable in between the bidding and purchasing stages.
As a result, contractors must scramble to get the materials on time and shuffle schedules to coincide with the arrival of the building materials.
For instance, if there is a delay in the delivery of the metal formwork, then the concrete can’t be poured, so you would have to reschedule the concrete delivery. You may end up doubling up on the trench work just so your employees have something to do in the interim.
While each building material has a slightly different story, here are the trends for each major building component.
Wood Prices Skyrocket
Wood prices have seen the most fluctuation and have been the most volatile.
Five years ago, lumber was just over $300 per 1,000 board feet. In May 2018, it hit a high of $629. It quickly lost half of its value, and then it danced around the $400 mark until March 2020, when it tumbled to $278 and remained around $300 for one quarter.
Construction boomed when governments decided the industry was a necessary service and therefore largely free from lockdown regulations. Governments saw the potential for construction to stimulate the economy and increased infrastructure investment.
Also, except for a few months at the beginning of the pandemic, where private investment scaled back or rescheduled construction projects, private investment into construction projects has remained high.
Plus, consumers sent home to work were buying wooden furniture to convert rooms into offices. Then, when they couldn’t go anywhere for entertainment, they started renovating other parts of their home. In the summer, many people installed pools (and decks) because they couldn’t travel.
By August, lumber had surpassed its 2018 high of $629. It climbed to $829 before dropping to just below $500 around Halloween 2020. Then, it climbed and climbed all through the winter and the spring until it reached its new all-time high of $1,670. As quickly as the price increased, it decreased again to $450 by August 2021. By October 2021, it was at $600.
When comparing the latest data on key wood product categories to five years ago, price increases aren’t as drastic as they have been recently.
Sept. 2021* Nov. 2016 change
Logging $219.7 $199.9 +10%
Lumber & wood products $292.7 $223.2 +31%
Softwood lumber $273.6 $198.8 +38%
Hardwood lumber $295.5 $222.7 +33%
Source: U.S. Producer Price Index
*All prices for September in this article are projected prices.
Building material prices decrease and usually cool off a little over winter, but forecasters expect wood prices to increase again in 2022.
Prices for Metals Go Up and Up
Meanwhile, like lumber, prices for metals have increased, but without similar decreases. It experienced all the highs of lumber but not all of the lows. For example, copper prices increase and decrease at a much smaller percentage.
Sept. 2021 Nov. 2016 change
Metals & metal products $316.1 $196.5 +61%
Iron and steel $402.9 $189.3 +113%
Copper and nickel ores $338.6 $538.8 +59%
Nonferrous metal ores $517.8 $279.2 +85%
Source: U.S. Producer Price Index
Prices for metals escalated the most when you compare prices over the last five years. However, in the previous six months, prices have remained fairly stable.
Contractors can expect a slight uptick and no reprieve from metals pricing.
Less Volatility with Concrete
Cement and concrete products have seen the smallest increase over the last five years.
Sep. 2021 Nov. 2016 change
Cement 274.6(P) 237.1 +16%
Ready-mix concrete 297.9(P) 254.9 +17%
Concrete products 295.9(P) 248.9 +19%
Construction sand, gravel
& crushed stone 381.2(P) 311.6 +22%
Source: U.S. Producer Price Index
Why have concrete product prices increased so little compared to other building materials? It is mainly because they don’t compete internationally.
Too heavy and too costly to transport long distances, there is a limit to concrete demand. Wood and metal products are shipped overseas, so local demand must compete with international demand, which drives up prices.
Adopting Tech to Offset Rising Cost
With little control over fluctuating building material prices, contractors are stuck to grapple with a moving target when bidding. They can’t cut the very materials needed to build, but can they mitigate some of these unknowns?
Many in construction must look for other ways to save money or make money to compensate for higher building prices.
For example, many contractors realize that the efficiencies gained by adopting construction tech can greatly impact their bottom line.
When you harness your construction project data, you can improve how you manage your project and improve communications between key stakeholders. This can decrease rework and therefore decrease construction costs and help you stay on schedule.
Think of it this way: every day represents thousands or tens of thousands of dollars in expenses, so if you can reduce the number of project days, you can improve the profit on any project.
Using a customizable, cloud-based project management platform can provide a single source of information. With a real-time dashboard, contractors can use actionable insights to drive efficiencies, optimization, and profitability.
By automating work and reducing rework, contractors can offset rising building costs and stay competitive in 2022.
Want to learn more about how adopting technology can help make your projects more profitable and easier to manage? Find out how Asite can help you create a single source of the truth. Learn more now.
Nathan Medcalf
Nathan Medcalf writes about technology, heavy equipment, and construction for numerous clients and has been published in more than 30 trade publications since 2006.
Asite Insights in your inbox.
Sign up for product news and our latest insights published monthly. It's a newsletter so hot, even global warming can't keep up.